1.真空成型・圧空成形とは
「真空成型(形)とは熱可塑性樹脂(適度な温度に加熱すると軟化して可塑性をもち、冷却すると固化する樹脂)のシートを加工する一つの方法で加熱軟化したシートを真空の圧力(型の微細な穴から空気を抜き真空にします)で変形させたまま冷却して成形品をつくる方法です。圧空成形の場合は、金型の周囲を密閉して枠を被せて圧縮空気を吹き入れて加圧成形する点が異なりますが、基本的には変わらない成型方法です。
2.真空成型機の構成
1.成型機の基本要素としては次のものがあげられます。
a.材料保持装置 b.加熱装置 c.型プラグを取り付けるプレス装置 d.真空装置又は圧空装置
2.補助装置としては次のものがあげられます。
a.材料の送り装置 b.成型品の取り出し装置
c.各部を動作させる空気減、油圧減、制御等の装置 成形品のトリミング、仕上げ装置
3.基本動作としての次の様な工程を必要とします。
常温の材料⇒クランプ⇒加熱軟化⇒成形,冷却⇒排気⇒成形離型⇒クランプ開く
⇒成型品取り出し⇒トリミング、仕上げ(成形と同時に仕上げる装置)
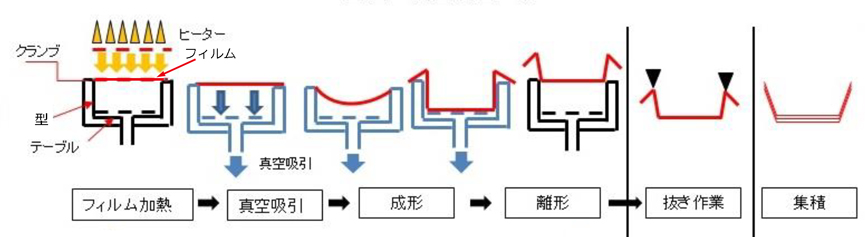
3.真空成型機の種類
成型機は、主に、一般用真空(圧空)成型機、ロータリー式真空(圧空)成型機、ライン式連続真空(圧空)成型機、ドラム式真空成型があります。各々に特徴がありニーズにより成型機を選択します。
一般用真空(圧空)成型機
成型機としては基本的な形態で、単発式とも呼ばれています。材料保持枠を中心にして加熱装置、金型テーブル、プラグテーブル等があり、材料をクランプ、加熱、成形、取り出しと材料が同一個所にとどまって成形を完了します。
真空成型は、加熱したシートを空気圧によって金型に密着させる成形方法ですが、真空の力だけでは成形が甘くなり大気圧以上の圧力は掛けることができません。真空圧空は同時に圧縮空気を掛けて成形するのでより精度の高い成形品が出来上がります。 肉厚も均等に成形できるため、強度があり容器として最適です。
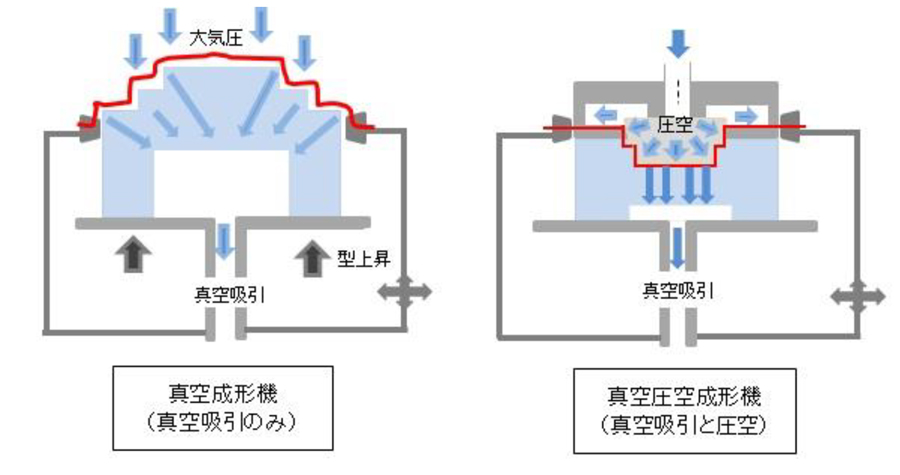
【特徴】
- 構成が単純であり操作も単純である。
- 時間が長くかかる。同一個所で材料クランプ、加熱、成形、取り出しするため、成形時間が長い。
- 大型成形品に適している。
- 少量から中量生産に適している。
- 試作品の製作に適している。
- 機械が安価である。
ロータリー式真空(圧空)成型機
クランプ、加熱、成形とそれぞれ別の個所に円周上に配置された各装置があり、カットされた材料を移動して成形します。
カットプレートを保持する複数個のクランププレートが軸を中心に回転して、材料供給、加熱、成形と各工程を経て成型品を得る成型機です。
【特徴】
- サイクルタイムが短く、工程が分業化されているため、一番時間が長く要する工程を通常の一般用成型機の1/3の時間で行える。
- カットプレートを材料とする大量生産の成形に適している。
- トリミング(自動仕上げ装置)工程など組み込んで完成品として取り出すこともできる。熱成形の後も穴あけ、外周トリミング等を続けて作業する機械もあり、従来数人掛かった作業を1名で完了させることができる。
ライン式連続真空(圧空)成型機
加熱、成形、トリミング(抜きの仕上げ装置)と各工程を一直線上に配列した成型機でロールシートを切断せずに成形するものが多いです。成形サイクルは目的によって異なりますが、加熱、成形、トリミング(成形と同時に抜き仕上げ装置)のいずれか最も時間を要する工程に合わせて成型を行います。
【特徴】
- ロールシートの厚みは通常0.1~1.2㎜程度であり、使用可能なシートの厚みは原則的にロールの巻き心経を大きくすれば制限はない。
- 成型サイクルは短く、比較的薄しシートを使用しているものが多くしたがって成形サイクルも短く、大量生産のものに適している。
【応用】
- 基本構成としては、加熱、成形、トリミング(抜きの装置)であるが成形後内容物を充填し蓋をかぶせてシールするブリスター包装機、タブレット包装機もある。
- 軽量容器の成形に最も適している。飲料カップ、果物包装、食品容器、冷凍食品容器等の成形に利用される。
- 特殊機として自動車内装品の成形に利用している。
- 同じ特殊機として冷凍機のクーリングタワーの内部部品を成形している。
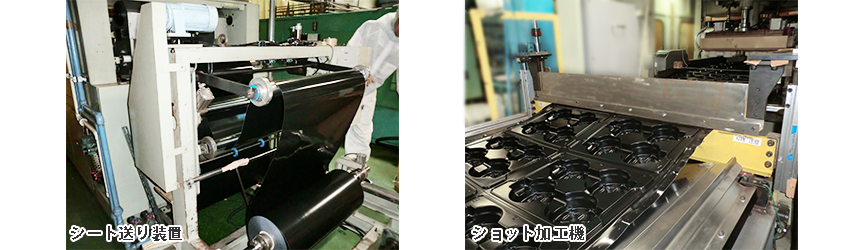
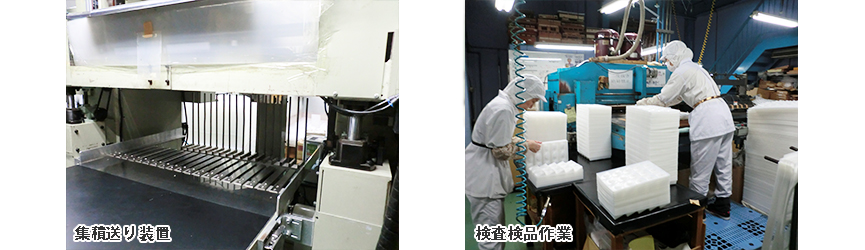
ドラム式真空成型機
円筒状又は多面角柱状に配置された型の周囲にロールシートを巻き付けて成型する機器です
4.真空成型品の取り数
- 生産数量の多いものは多数個取り、生産数量の少ないものは少数個取りにします。成型品の数量の多いものは成型機の能力をできるだけ利用して多数個取りにします。生産数量の少ないものは型代の償却を考えて少数個取りとします。
- 1ショット当たりの成形費用は大面積でも小面積でもほとんど同じです。1ショット当たりの成形コスト(材料費と型の償却費を除いた場合)は、同一成型機を使用した場合は多数個取りでも少数個取りでもほとんど変わらないです。したがって数量の多い時は多数個取りの方が有利です。
5.真空成型品の材質による収縮率の差
使用する材料により収縮率が異なりますので、前もって計算しその分だけ成形型の寸法大きく製作する必要があります。収縮率の標準値は下記の通りです。
塩化ビニール | 3/1000~4/1000 |
ポリスチレン | 4/1000~5/1000 |
二軸延伸ポリスチレン | 5/1000~6/1000 |
発砲ポリスチレン | 4/1000~5/1000 |
ポリプロピレン | 15/1000~16/1000 |
ポリエチレン | 20/1000~25/1000 |
6.真空成型の型について
真空成形(真空成型)の凸金型について
凸型は平面の強度が強く現れて上からの圧力に耐えられるが側面が少し弱く成型されます。一般的にはブリスターパック等に用いられ天面の強度が必要な成形品に最適です。金型の費用が安く取り数が凹型よりは少ないです。
真空成形(真空成型)の凹金型について
凹型は周りの縁が強く平面の部分は少し薄くなり弱い。一般的には食品トレー等に用いられ金型の費用は凸型より少し高く取り数は凸型より多く取れるため、コストが安く上がります。
凹凸型プレス成型の金型について
凸金型と凹金型の弱点を補う成形方法で凸凹金型を同時に使用して成形する方法で天面と側面と均等に強度を出してバランスの良い成形品が出来上がります。だだし、金型代は片面より両面のため製造コストはかかります。
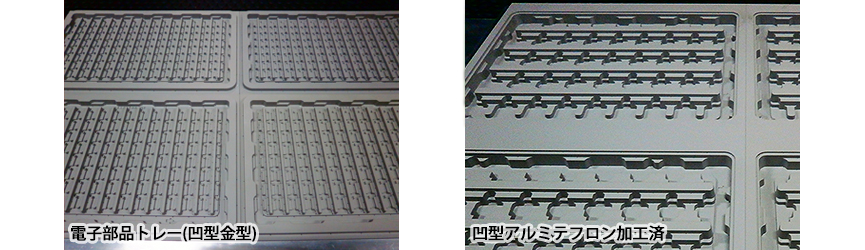
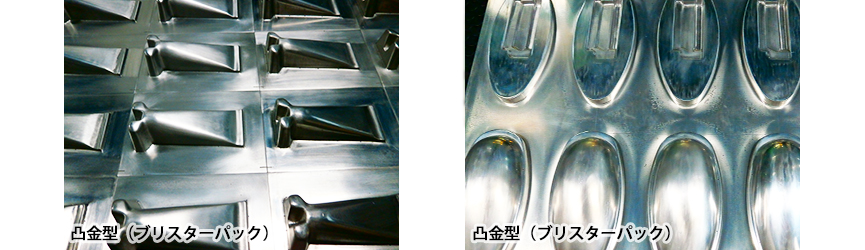
7.型素材の選定について
製作工場の得意と材質を選ぶことが重要です。鋳造型を使用するときは鋳造所の得意とする材質、加工の素材を選んで作成します。型は大型のものはむろん小さいものでも型の取り付け、取り外しが容易であるよう軽いものが良いです。
木材型
よく乾燥した木目の緊密な木材を用います。鋳造用の木型材料としては、ひのき、ほう、ひめこまつ、赤松、かえで、マホガニー、ヒッコリーが適しています。
【特徴】
- 安価である。材料費、加工費共に安く製作日数も短い。
- 表面状態が悪い。成型品の表面に木目が移る。
- 少量生産向きである。成型時の熱によって乾燥し、成形を続けるとひび割れが起こることがある。
- 成形サイクルが長い。熱伝導性が悪いから冷却時間を長くする。
- ネルは伝導性が悪いからドラッグラインは強く表れない。
- 離型後の変形が少なく試作品向きである。
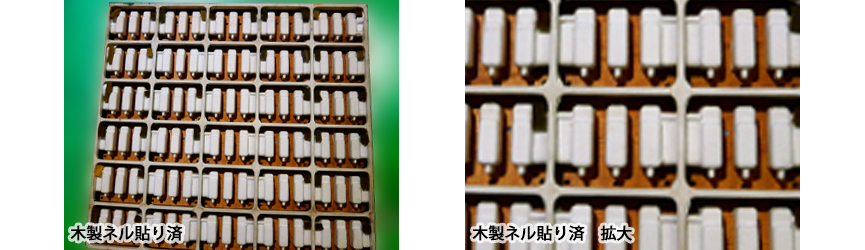
人工木材型
【特徴】
- 人口木材型は密度の高い発泡合成樹脂で木型と異なり成形に依って型には方向性やひび割れが起きない。
- 発泡合成樹脂のため、NC機械対応が容易で寸法精度形状に向いている。
- 熱伝導性が悪いので成形サイクルが長く量産型には不向きである。
- 人口木材型は発泡合成樹脂のため、表面のザラツキがあるため、成形品は透明性に欠ける(試作品向きである)。
- 熱伝導性が悪く冷却も悪いので成形品が変形しやすいことがある。
- 材料のコストや加工性に優れていることや修正も容易であるから安価に作成できる。
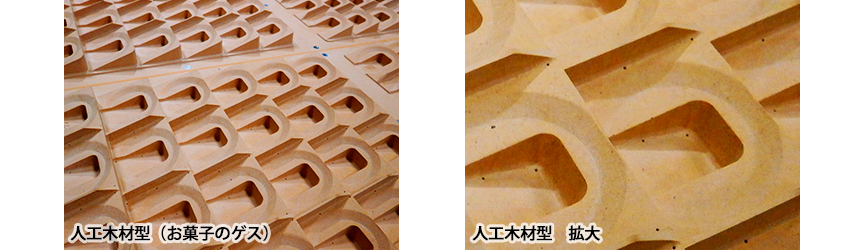
石こう型
【特徴】
- 泡を表面に出さなければ平滑にも微細な模様も表現できる。
- 肉の薄いものや角物は欠けやすい。表面状態は良く、耐久力もかなりあり、少量生産、試作品、中量生産にも品質良い成型品をつくることができる。
- 成形サイクルは長く、ドラッグラインはあまりつよくあらわれない。変形が少なく、材木と比較すれば熱伝導度は約10倍である。
- 試作、少量生産多品種向きで安価で作成できる。
熱硬化性樹脂型
材料としてはエポキシ、ポリエステル、フェノール等の樹脂があり、それに補強材、増量剤を入れて使用することが多いです。
【特徴】
- 鏡面仕上げは出来ないが非常によく仕上がる。
- 木材、石こう、と比べてかなり強度は高く量産用として使用できる。
- 冷却時間が長い。ドラッグラインはあまりあらわれない。離型の変形は少ない。
- 熱膨張が大きく、成型を続けると温度が上がり膨張したりひずみができたりする。精度を要求される成型品には不向きである。
- 型の修理、デザインの変更が容易であり、接着力が強く加工性も良いから容易に修正ができる。
金属型
鉄、アルミニウム合金、亜鉛合金、砲金等が使用されますが、それぞれ特徴をあり選定が難しいです。傾向としては小型のものは亜鉛合金砲金、アルミニウム合金等が良く、大型のものはアルミニウム合金が適しています。
【特徴】
- 鉄はその他の金属と比較してかなり安価あるが錆が発生するのと排気穴の加工が困難なためあまり使用しない。
- 鋳造したままの状態の表面は亜鉛合金が最も良いが、圧力鋳造をすればアルミニウム合金でもほとんど仕上がりが不要な程度にできあがる。
- 砲金、亜鉛合金はともに切削性が良く問題はないが、アルミニウム合金は加工性が劣る。
- 小型のものは重量による影響はないが大型のものはアルミニウム合金が軽いため適している。
- 熱伝導性がよいから型温度の調節が比較的容易にでき、高速成型に適している。
8.型の温度調節方法
型の適温は材料によって大きく異なり30~90度の範囲です。対策としては大別すると型に接していな側から空気や水を吹き付けて冷却する方法と、型を冷却して型から熱を吸収し冷却する方法であります。
- 型に直接水を通し冷却する直接型は、冷却水を通すのに型に穴を開け水路を設けて冷却する方法と型の外面にウォータージャケット(冷却装置)を取り付けて冷却する方法である。
- 型を冷却版に取り付ける方法は、冷却水を通した基盤に型を密着させ間接的に冷却する方法は基盤の制作は容易でコストも低いが型と基盤との熱伝導性が悪く冷却効果が悪い。
- 成形温度の高い樹脂は温水を通し温度を上げある程度の温度を保たないとよい成型ができない。
- サイクルアップのため、チラーユニットで冷水を作り5度程度の水を通し冷却する場合もある。
9.抜き勾配(ティパー)について
- 凸型成形では成型品が冷却すると型を締め付けるように収縮するから離型が困難になるので、一般的には2度程度以上の抜き勾配(ティパー)を付ける。
- 凸型の側壁は平滑に仕上げておくと離型しやすく、特に流動性の高い材質はポリエチレン、ポリプロピレンには必ず必要である。
- テーブルの下降速度を遅くするとともに離型エアを吹き出しながら下降させ、型の頂部に離型エアの穴を開けて置くと成型品が変形しないで離型が容易である。
- 凹型成形では成型品が冷却とともに型から離れるように収縮するため、離型は容易である。
- 機械的にノックアウトを付けてアンダーカットのある成型も可能である。
10.射出成型と比較して真空成型・圧空成型のメリットとデメリット
真空成型(圧空成型)は、射出成型と比べると次のようなメリットとデメリットがあります。
【メリット】
金型の納期が早いのか?
- 試作納期3~6日程度です。
- 金型納期3週間位です。
金型の価格は?
- 加工が容易であり材料費も安価です。
- ブリスターパック等ほど1/10位でできあがります。
デザインや形状の修正が簡単か?
- 金型の変更や修理等が容易に行えます。
- 抜き型とは別工程のため修正が不要の場合もあります。
材料の厚みが変更が可能か?
- 試作品から厚みを変えて製作が可能です。
- 試作品からプラグを使用して製作が可能です。
凹型凸型でも成形はできるか?
- 用途に応じて特徴を生かすことが可能です。
- 一般的にブリスターパックは凸型で行います。
- 一般的にはトレーは凹型で行います。
少ロット・多品種の生産が可能か?
- 少数生産と取り合わせが可能です。
- 試作品の場合10個~100個も可能です。
異なった材料の試作成型は出来ますか?
- 材質PET、PS、PP、ABS、PPF、等の異色の成型も可能です。
【デメリット】
金型に盛り付けすることができますか?
- 金型に0.5㎜、1㎜、2㎜、の盛り付けは不可能です。
材料費自体のコストは高いのか?
射出成型はレジンそのまま使用するのですが真空成型はレジンを一度シート 状に押し出して二次加工するため素材のコストがアップします。
生地ロスの費用はなぜ割高になるのか?
成型した物は必ず抜き仕上げが必要でクランプ、ロスの不要な部分の抜き仕上げが必要となります。
形状により部分的に肉厚がなぜ変わるのか?
製品の高さ(深さ)等によりコーナーが伸ばされて薄くなりやすいです。
成形品の肉厚が内寸と外寸が異なるのか?
金型に面した側としていない側とでは厚みの精度にバラ付きが発生します。
成形品の肉厚が内寸と外寸が異なるのか?
細かいマスの深い形状の精度の高い成型は不可能です。
11.失敗しない真空成形の設計のTips
マツバではお客様のニーズにお応えするため、色々な経験より設備機器の充実とノーハウの蓄積を行っております。ここでは、Tipsの一部を紹介しております。
アンダーカットのある成形品
アンダーカットのある成形品は、アイスクリームの製品とか勘合式の成形品等、密封容器に使用されていますが、成型方法、離型方法、離型手段として次のような特徴を挙げることができます。
- 金型の凹型にわずかなアンダーカットのへこみを付けて材料の収縮によりそのまま成形すればよいです。
- 金型の凸型にアンダーカットのある成形品はノックアウト装置で成形品を突き出します。無理をして突き出しても成形品が破れたり変形したり白化しないものは、ノックアウト板かノックアウト棒で突き出せば離型はできます(この方法はアイスクリームカップの成型に用いられています)。
- 大きなアンダーカットのある成形品は割型にします。無理をして離型をすると破れたり変形したりするものまたは、離型できないものは割型にして離型します。
- 離型時にエアーを強くし、型とシートの間に吹き付けて成形品を型から離型をさせます。
- クランク枠で周囲を挟んで型を下降させて離型をすることもあります。
- 機械的にノックアウト機構によって突き出す方法です。
ノックアウト機構はアンダーカット個所にすると良いです。
ノックアウトは通常エアーシリンダーを使用していますが多数個取りでアンダーカットの大きいものをエアーシリンダーの推力不足が原因で離型できないこともあります。 - 割り型を使用する場合は、最初から型にヒンジを付けてアンダーカット部分を動くように作成する金型です。
プラグを使用する成形品の特徴と注意
プラグは深絞りのときの肉厚調整を目的とします。
- 成形途中まで直接加熱シートと接触してもシートの温度を下げないこと。
- 肉厚調整のため、形状変更が容易にできる材質及び構造であること。
- シートの滑りを適度にするために摩擦の低い材料を使用するか、直接面積の少ない毛ば立った材料を表面に使用すること。
- 硬い木目の少ない良く乾燥した材木を削りそのままプラグとして使用すること。
- 木製プラグの表面にフエルトかフランネルを張り付けます。コストが安く、スタート時から良い成形品がえられるので最も多く使用されています。
- 加熱過度のときは、シートの引張り強さが小さく、プラグの先端で肉を底部へ持っていくため側壁が薄くなります。加熱を減らしてドローダウンを少なくすることが必要です。
- プラグの押し込み過度のときは、プラグ効果の出し過ぎと押し込み量を減らすことが必要です。
- プラグ形状が不適当なときは、プラグが大き過ぎるたり、先端のRが小さい場合やプラグの形を型に合わせ過ぎたときなどがあります。
- プラグ速度が遅すぎるときは、シートがプラグに接触している時間が長く、シートが冷えてプラグ効果が出過ぎる場合です。
プラグ速度を早くすることによって解決します。 - プラグ温度が低いときは、プラグ効果が出すぎるためヒーターを付けるかネルを張り付けて自然に温めるとよいです。
- 真空開始のタイミングが早すぎるときは、プラグの押し込み量不足が考えられ、プラグを長くしてみると改善します。
ブリッジが出来る原因
ブリッジの出来る原因は雄型成型において、雄型で突き上げられて一旦伸ばされたシートが型に密着する過程で縦方向には伸ばされますが、横方向には縮められるために両端からシートが寄り集まって余った分がブリッジとなります。ブリッジの出来る原因としてもう一つ張力の差があります。角形の時の角やお互いに接近した雄型の最も近い箇所はその付近のシートの伸び率が一番大きく張力が大きいので成形吸着するときに遅れて型に近づき、その場合横方向に余ったシートがあるとブリッジが発生いたします。
- 雄型の勾配を緩やかかにすればブリッジは取れます。
- 立ち上がりのコーナーにRを付けて余ったシートを吸収させるようにします。
- 多数個取りの場合はプラグで押さえつけてブリッジを解消するようにします。
- 加熱過度の場合は加熱オーバーのため、シートに自己収縮の力が減りブリッジが出やすくなります。
加熱を減らしてシート温度を下げることが必要です。
安定した加熱をするには
成形条件が変動すると不良品が発生するか、不良品の一歩手前の状態になります。不良品を出す前にその原因を取り除く必要があります。不安定な加熱もその一つで、加熱の不適による不良品が最も多くしめています。さらに精査すると電圧の変動と共に不良品が発生している場合があります。 対策として自動変圧調整器を付けて成形をすると不良率が低下します。
【原因の対策】
- 電圧の変動
- 気温の変化:気温の変化以外に加熱器の中へ風を吹き込んでヒーター温度を低下させたり雰囲気温度が下がったりすることがあります。
- シートの温度の差:供給シートの温度の差は材料置場と成型機付近との気温の差が大きいときに問題になります。冬季は材料を前日から成型機の横に置くか少なくとも成型機のある工場内にはこび込んで置くことが必要です。
- スタート時から一定温度に安定するまでの変化が大きいので、スタート時は少し加熱時間を長くし、順次短縮すれば良いです。
- 成型機の働作時間のばらつき:駆動用空気源の容量不足による空気圧の変動があります。
- 全く加熱条件の分かってない材料で成型を始めるときは、垂れ下り始め時か、その数秒後が成形に最も適した温度といえます。
【加熱不測の時】
- 凹型のコーナーが甘くなったり、金型に密着しなくなります。
- アンダーカットのある部分が丸くなり寸法精度が悪くなります。
- 型の面が傷や排気穴の跡がつかなくなります。
- 成形品の表面光沢が良くなります。
- 偏肉が少なくなり冷却時間が長くなる場合があります。
【加熱不足の対策】
- 加熱器の温度を上げたり、加熱時間を長くします。
- 真空もれや不足していないかチェックします。
- 排気孔が不足している場合は穴が詰まっている場合があります。
- 排気孔の径を大きくしたり、排気穴を掃除します。
【加熱過度の時】
- 偏肉、特に側壁が薄くなります。
- ブリッジが発生しやすくなります。
- 排気穴の跡が成形品にできてしまいます。
- プラグアシスト成形のとき、フランジ部分にしわが出たりパンクしたりします。
- 加熱時にシートが垂れ下ります。
【部分的に不良品が発生する時】
加熱時にヒーター内へ風が入り部分的に加熱むらが起こっている場合が多いです。
金型温度条件に付いて
真空成形において金型温度条件は、製品の仕上がりを大きく左右します。
【金型温度が低い時】
- 冷却時間が短縮されることが可能になります。
- ドラックラインが表面に強く表れます。
- 凹部のコーナーが充分に成形が出来ないことがあります。
- 表面が肌荒れ起きやすいです。
【金型温度が高い時】
- 冷却時間が長くすると必要があります。
- ドラックラインが無くなり美しく仕上がります。
- 凹部のコーナーが型再現性が良くなります。
- 表面が滑らかに綺麗になることができます。
【樹脂に対して温度条件】
- 金型温度を高くする樹脂は、ポリエチレン、ポリプロピレン、ポリカーボネートで、これらの樹脂は温調器を接続して80℃前後に温めてから始動することが望ましいです。
- 金型温度が中程度の樹脂は、ポリスチレン、ABS、これらの樹脂は成形開始後50℃程度になってから冷却水を通しその温度を保持します。温調器でウオームアップすればさらに良好な仕上がりととなります。
- 金型温度を低くする樹脂は、PVC、A-PETで、これらの樹脂は成型前に温調器を通して規定温度より僅か低い温度までウオームアップしてから自動制御をするようにします。
【金型再現性不良】
- 排気穴の不足、排気穴の位置不良、排気穴不足によって、型再現不良おこるのは薄いシートの成形に多く、排気速度が遅くシートが型に密着する前に冷めてしまうことで発生します。
- 無効空間を少なくするように型を改造して防ぐことも可能です。
- 空気配管系が詰まっていると、排気抵抗が大きくなり真空が上がりにくくなります。
- 配管途中にゴミが詰まっていないかを確認し、ストレーナ、フィルタを掃除することも重要です。
【真空漏れ】
真空成型において真空漏れのトラブルは非常に多く、またその原因を見つけ出すのがなかなか困難なです。ここで上げる要点を順次 チエックすることで原因発見と対応が可能になります。
- 真空成形機には真空計が付いていますが、真空ポンプと真空サージタンクの回路に付いている計器を成型時の動きとともに観察すると漏れに気づきことができます。
- 金型とテーブルの間のパッキンが破れて漏れることもあり、注意が必要です。
- 型とシートとの間の漏れは、突き上げ不足で凹型成型ではシート面より2~3㎜突き上げれば吸着し、エアーが漏れになります。
- ロールシートの連続成形機の場合、送り量が不足していると未加熱部分が型のコーナーに乗り、エアータイトができないことがあります。
- 型とプラグが接近しすぎて破れることに注意が必要です。
- 型再現性が悪く凹部のコーナーが密着しないものは、まず、原因を真空漏れか加熱不足かに区別することが重要です。加熱不足と見分けるために一度加熱過度になるような成形をしてみて余り改善されないようであれば、真空漏れと判断をすることができます。
【ドラグライン】
ドラックラインはチルマーク(冷却跡)とも呼ばれる通り、加熱された軟らかいシートが型やプラグに最初接触した時にその部分だけが冷えて伸びが悪くなり、線状に厚くなる現象です。
このドラグラインは熱成型においては解消が最も難しい現象といえます。
- 型温を上げてシートの冷却を少しでも遅くします。
- 型の天部のコーナーを滑りやすく平滑になるようにします。
- 型の頂部のコーナーのRを大きくして接触圧力を減らします。
- プラグの温度をシート温度に近ずけ冷却を防ぎます。
- 型やプラグの速度を上げて接触時間を減らことで改善することもできます。
【排気穴の径】
- 穴径はシートの材質、厚み、表面に対する美観の要求度等によって異なります。
- 硬質塩化ビニル、スチレンモノマー、ABS、アクリル、A-PET等は、穴径は0.8Φで、ポリエチレン、ポリプロピレン等は0.4~0.5Φ程度がベターです。
- ポリエチレン、ポリプロピレン等では径が大きすぎると孔の中に樹脂が流れ込んで突起が成形されたり、穴が開いたりするので注意が必要です。
- 凹型のコーナーに集中して開けることで成型時にシートが型と接すると成形が綺麗に仕上がります。